Top 5 Industrial Workplace Hazards and Prevention Measures
April 10, 2023
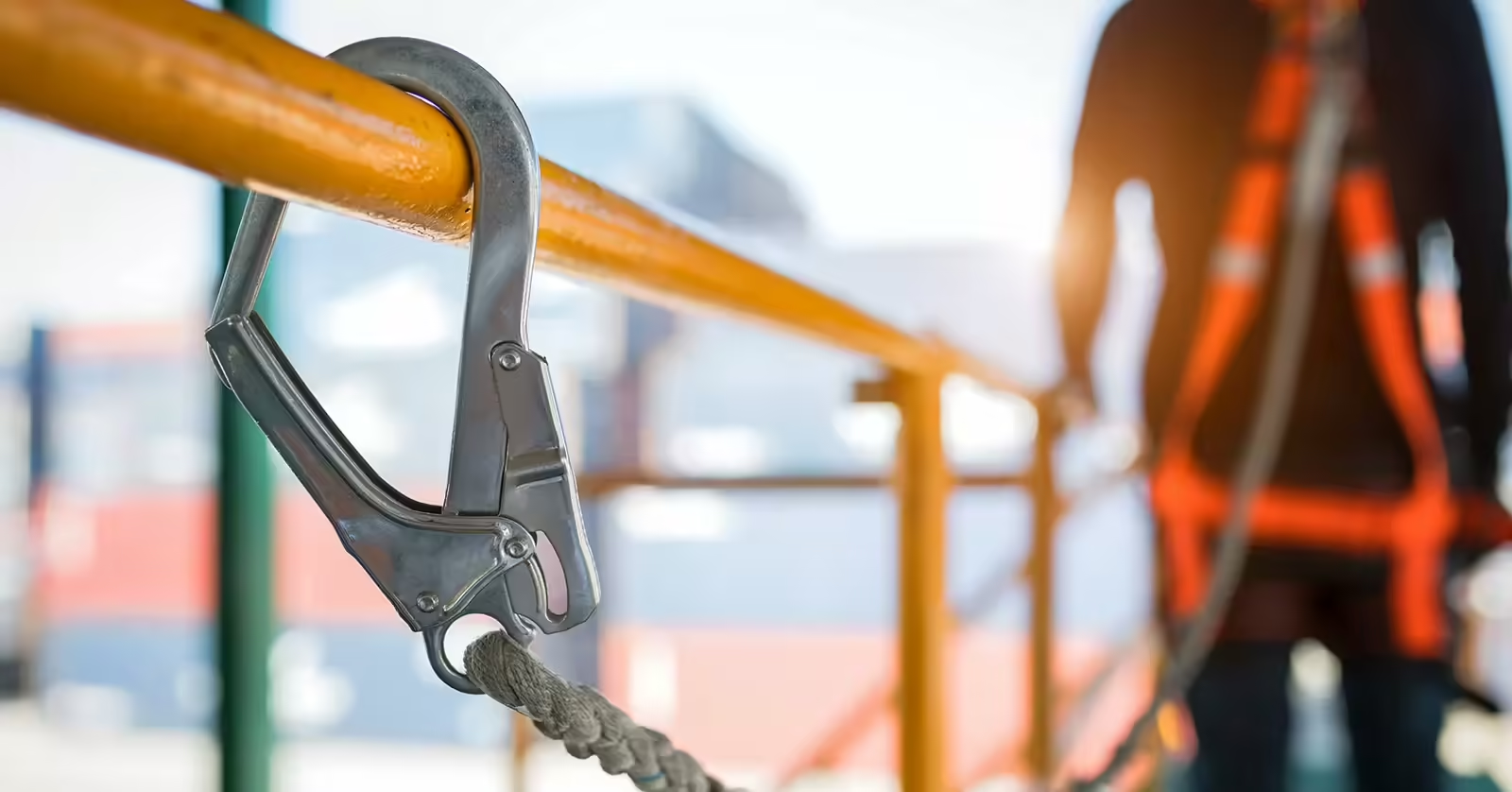
Industrial workplace hazards are often exposed to workers that can cause serious injuries or even fatalities. According to the Bureau of Labor Statistics, there were 5,333 fatal workplace incidents in the United States in 2019, and 15% of them occurred in the manufacturing sector. Therefore, it is important for industrial employers and employees to be aware of the potential risks and take preventive measures to ensure a safe and healthy work environment.
This article discusses the top five industrial workplace hazards and prevention measures, based on the Occupational Safety and Health Administration (OSHA) standards and workplace safety recommendations.
Machine Guarding
Machine guarding is the use of physical barriers or workplace safety devices to protect workers from contact with moving parts of machines or equipment that can cause cuts, amputations, burns, or crushing injuries. OSHA requires that machines be guarded to prevent workers from reaching into or through the danger zone, where the machine performs its operation. Some examples of machine guarding are fixed guards, interlocked guards, adjustable guards, self-adjusting guards, and presence-sensing devices. Machine guarding should be designed and installed according to the manufacturer’s specifications and instructions, and should not create additional hazards or interfere with the operation of the machine.
Lockout/Tagout
Lockout/tagout is the practice of controlling hazardous energy sources during the servicing or maintenance of machines or equipment. Hazardous energy sources include electrical, mechanical, hydraulic, pneumatic, chemical, thermal, or other forms of energy that can cause harm to industrial workers if released unexpectedly. OSHA requires that workers follow a specific workplace safety procedure to isolate and lock out or tag out the energy sources before performing any work on the machines or equipment.
The procedure should include preparing for shutdown, shutting down the machine or equipment, isolating and locking out or tagging out the energy sources, verifying the isolation, performing the servicing or maintenance work, removing the lockout/tagout devices, and restoring the machine or equipment to normal operation.
Hazard Communication
Hazard communication is the process of informing workers about the identity and hazards of chemicals they may encounter in their work area. OSHA requires that employers develop a written hazard communication program that includes a list of hazardous chemicals in the workplace, safety data sheets (SDSs) for each chemical, labels and other forms of warning for containers and pipes containing hazardous chemicals, and training for workers on how to handle and dispose of hazardous chemicals safely. Workers should have access to SDSs and labels at all times, and should follow the precautions and instructions provided by the manufacturer or supplier of the chemical.
Respiratory Protection
Respiratory protection is the use of personal protective equipment (PPE) to protect workers from inhaling harmful substances in the air. These substances may include dusts, fumes, mists, vapors, gases, or biological agents that can cause respiratory diseases or impairments. OSHA requires that employers establish a written respiratory protection program that includes a hazard assessment, a selection of appropriate respirators for each hazard, a fit testing and training for workers who use respirators, a medical evaluation for workers who need respirators, a maintenance and cleaning of respirators, and a periodic evaluation of the program’s effectiveness. Workers should wear respirators whenever they are exposed to airborne contaminants that exceed the permissible exposure limits (PELs) set by OSHA or other regulatory agencies.
Fall Protection
Fall protection is the use of systems or methods to prevent workers from falling from elevated surfaces or into holes or openings in floors or walls. Falls are one of the leading causes of fatal work injuries in industrial workplaces, especially in construction and roofing activities. OSHA requires that employers provide fall protection for workers who are working at heights of four feet or more in general industry, six feet or more in construction industry, or any height above dangerous equipment or machinery. Some workplace safety examples of fall protection are guardrails, safety nets, personal fall arrest systems (PFAS), positioning device systems (PDS), warning line systems (WLS), controlled access zones (CAZ), safety monitoring systems (SMS), and covers for holes or openings.
Contact An Experience Industrial Injury Lawyer For A Free Consultation
In conclusion, industrial workplace hazards can endanger the lives and health of industrial workers. Therefore, employers and employees should comply with OSHA standards and recommendations to prevent injuries and illnesses from these hazards. By implementing workplace safety such as machine guarding, lockout/tagout, hazard communication, respiratory protection, and fall protection measures in their workplaces, they can create a safer and more productive work environment for everyone.
If you are injured in an industrial workplace accident, the best thing you can do is contact a qualified industrial accident lawyer for a free, confidential consultation to walk you through your options going forward and which one would work best for your situation. Do not hesitate to contact Morrow & Sheppard, LLP today to discuss your potential work injury claim and the best way to resolve it going forward.
Hogan Leatherwood is an experienced trial and personal injury attorney representing individuals and their families who have suffered catastrophic injuries such as brain injuries, spinal cord injuries, burn injuries and wrongful deaths of loved ones caused by the wrongful business practices of large companies and corporations. Hogan is regarded throughout the legal industry as a zealous and relentless advocate for his clients. Learn more about Hogan.
- Home
- |
- Workplace Accidents
- |
- Top 5 Industrial Workplace Hazards...